Effects of Heat Treatment on Material Integrity
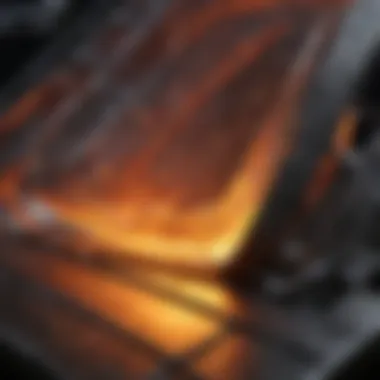
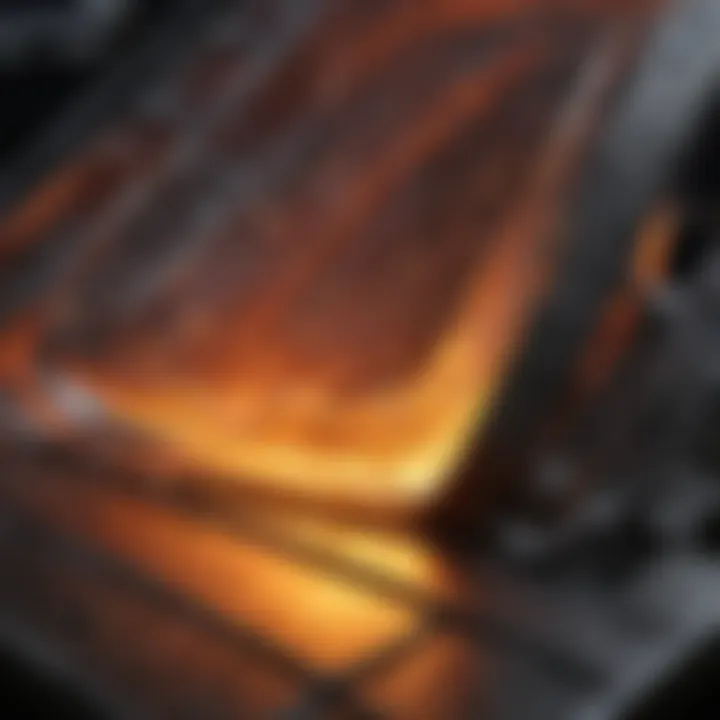
Intro
Heat treatment is a fascinating aspect of material science that can significantly alter the properties of various substances. Whether it's metal, wood, or plastic, exposing these materials to heat can lead to enhancements in structural integrity or, conversely, damaging effects if not properly executed. Understanding these processes is key for homeowners, DIY enthusiasts, and professionals who engage with these materials, particularly in contexts like pest control and construction.
When we talk about heat treatment, we often delve into methods like annealing, quenching, or tempering, each with its own purpose and outcome. The ability to control the heat treatment process allows you to tailor a material's characteristics, which can boost a project's overall effectiveness. But beware, improper application can yield undesirable results, resulting in compromised material integrity.
This article is designed to shed light on the various impacts of heat treatment, from its benefits to the potential pitfalls. We will explore how heat interacts with different materials, identify visual signs of damage, and provide strategies to mitigate risks effectively. By the end of our journey, you’ll have a clearer understanding of why mastering heat treatment is essential for anyone involved in construction or pest management.
Overview of Heat Treatment
In the realm of materials science and engineering, heat treatment plays a pivotal role. It's not just a fancy term tossed around in industrial circles; it dictates the strength, durability, and overall performance of various materials. Heat treatment refers to a controlled process involving the heating and cooling of materials, usually metals or alloys, to achieve specific properties. This is crucial for applications ranging from automotive components to household items.
Understanding heat treatment is essential for homeowners and DIY enthusiasts alike, especially those venturing into home improvement or construction tasks. By grasping what heat treatment entails, individuals can make more informed decisions when selecting materials for their projects.
Definition of Heat Treatment
Heat treatment can be defined simply as the process of heating and cooling materials in a specified manner to change their physical and sometimes chemical properties. The exact temperature and duration of heating depend heavily on the type of material being treated and the desired outcome. For example, steel can be heated to bright red-hot temperatures and then cooled rapidly to enhance its hardness, while other metals may require more gradual cooling for increased ductility.
The intricacies of heat treatment are fascinating; for instance, the austenitizing phase is where steel transitions to a non-magnetic phase upon reaching certain temperatures. The ability to reshape and reinforce materials through this technique makes it invaluable in various industries.
Purpose of Heat Treatment
The purpose of heat treatment can best be summarized by its main objectives:
- Enhancing Strength: One of the primary goals of heat treatment is to increase the strength of materials. By manipulating the microstructure through different heating and cooling techniques, materials can be made stronger and more resilient.
- Improving Ductility: Heat treatment does not only toughen materials; it can also improve their ability to be molded or shaped without breaking. This is key in construction, where flexibility is often required.
- Relieving Stresses: For new materials, internal stresses can develop during manufacturing. Heat treatment helps relieve these stresses, preventing future warping or cracking.
- Coating and Finishing Enhancements: Many heat treatment processes refine surface properties, resulting in better corrosion resistance or aesthetic finishes, important to homeowners keen on durability and appearance.
This approach not only broadens the capability of metals and plastics but also helps in tailoring materials for specific applications and conditions.
"Understanding heat treatment can give you an edge in selecting the right materials for your home improvement projects and help avoid costly mistakes."
Whether you’re a seasoned pro in construction or someone just starting with DIY, knowing about heat treatment prepares you better for the challenges ahead. It’s about so much more than just heat; it's about crafting materials that genuinely perform.
Material Types Affected by Heat Treatment
Understanding the differences in how various materials respond to heat treatment is crucial for anyone looking to use or manipulate these substances, especially in fields like construction and DIY projects. Each material—be it metal, plastic, or wood—possesses unique properties that dictate how it will change when subjected to different temperatures. This section dives into the nuances of these materials, examining their characteristics, the processes they undergo during heat treatment, and the potential benefits or drawbacks in using them.
Metals
Types of metals
When discussing the types of metals that undergo heat treatment, it’s not just about the common players—aluminum, steel, and copper. Each metal comes with its quirks that can lead to different outcomes during the treatment process. Aluminum, for instance, is lightweight and resistant to corrosion, making it a go-to for many structural applications. It also retains its strength, even when heated, unlike some other materials that buckle under the pressure of high temperatures.
On the other hand, steel is a heavyweight champion in the realm of metals. Its alloys, like stainless steel, provide exceptional toughness after heat processes. A key characteristic of steel is its ability to gain hardness through techniques such as quenching, reinforcing its versatility in diverse applications.
In short, metals like aluminum and steel are beneficial in heat treatment scenarios due to their adaptability and strength.
Heat treatment processes for metals
Now, addressing the processes, we often hear terms like annealing, quenching, and tempering. Each has its own role in enhancing metal properties. Annealing, for example, is known for softening metals and making them easier to work with. This is particularly advantageous in manufacturing, where a simpler workpiece can save time and reduce tool wear.
Quenching, which involves cooling a hot metal rapidly, often leads to increased hardness—great for cutting tools or structural applications that need to endure wear and tear. However, this process can introduce internal stresses, making detailed understanding essential.
Unique facets of these processes—like the risk of fracturing due to rapid cooling—align well with the overall goal of optimizing material performance while addressing potential hazards in applications.
Common vulnerabilities
Despite all their strengths, metals do have vulnerabilities during heat treatment. Common issues include warping, cracking, and changes in corrosion resistance. These problems can often arise if the temperature isn’t controlled properly or if the metal is subjected to uneven heat distribution. Warping can lead to significant fitting issues in construction, while cracking can render a material completely useless.
Understanding these vulnerabilities allows homeowners and professionals alike to mitigate risks before they become costly problems. Each treatment process comes with its own set of potential complications, and recognizing these can lead to better planning and improved material integrity.
Plastics
Thermoplastics vs Thermosets
When we switch gears to plastics, the distinction between thermoplastics and thermosets is significant. Thermoplastics can be reheated and reshaped multiple times without altering their chemical structure. This flexibility makes them suitable for a variety of applications, from packaging to intricate moldings in automotive parts. Conversely, thermosets form irreversible bonds during the curing process, meaning they harden permanently and cannot be re-molded once set.
This permanence is advantageous for items needing durability like electrical insulators, but makes the material inflexible with heat. With these differences, understanding the application will guide the choice that aligns with project needs.
Effects of temperature on plastics
The way temperature interacts with plastics is another area where caution is warranted. Increased temperatures can lead to softening in thermoplastics, potentially causing deformation under load. An example would be a plastic item left in a hot vehicle; it may lose its shape entirely. For thermosets, while they resist reshaping, excessive heat can still lead to thermal degradation or release of hazardous byproducts.
Recognizing how temperature affects these materials can ultimately influence product design and expectations regarding longevity and performance.
Long-term impacts
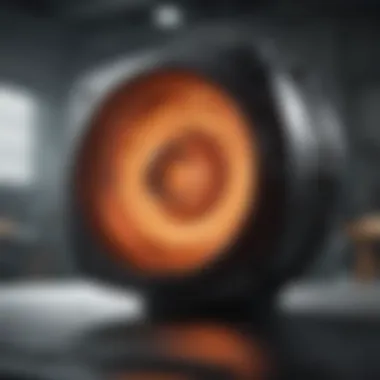
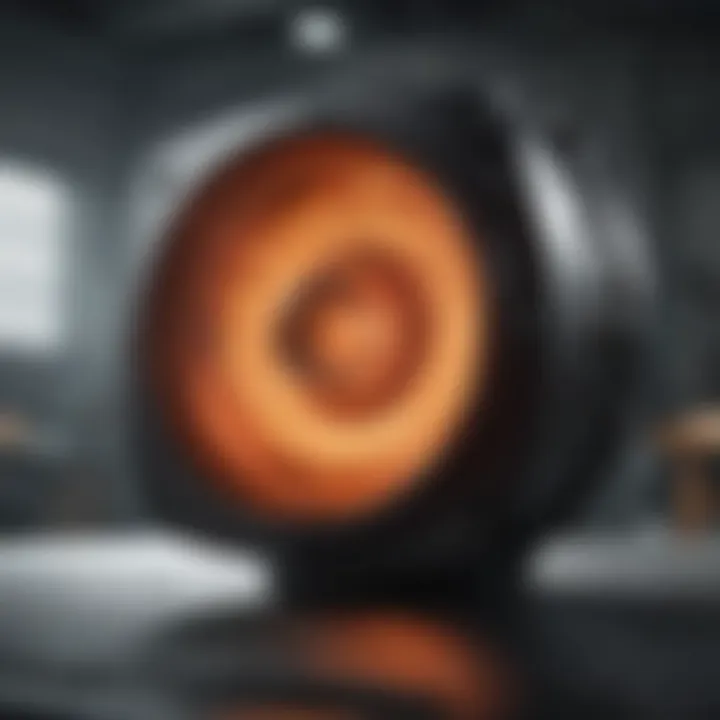
Finally, long-term impacts of heat treatment on plastics cannot be overlooked. Over time, exposure to sustained heat can lead to changes such as embrittlement—most noticeable in materials left in sunlight or fluctuating temperatures. This can greatly affect safety and functionality in household items or structural components, implying that constant monitoring is essential.
Awareness of these long-term concerns can guide homeowners in choosing plastics that not only fit their immediate needs but can also withstand the test of time.
Wood
Wood properties and heat
When it comes to wood, heat treatment can enhance various properties, leading to increased resistance to pests and decay. Heat stabilizes wood by removing moisture, which is often the hidden enemy in many wooden structures. This process leaves wood less prone to changes in its dimensions, thereby improving overall reliability.
However, the unique feature of this treatment is that excessive heat can also lead to weakening of the fibers, impacting structural integrity.
Changes in structure and function
Heat treatment can change wood in its very essence. As the temperature rises, its structure may undergo a transformation at the molecular level, leading to improved dimensional stability. This characteristic is invaluable, especially in areas where humidity levels fluctuate. Whereas untreated wood may swell or shrink dramatically, heat-treated wood tends to keep its shape and size, providing a reliable alternative for various applications, from flooring to outdoor furniture.
On the flip side, the heating process can sometimes lead to a darker coloration, which might not be appealing for everyone—an important consideration when selecting materials for visible structures.
Potential for warping and cracking
One major concern with heat treatment of wood is the potential for warping and cracking. If the wood is heated too quickly or unevenly, it can lead to severe distortion that compromises its aesthetic and functional performance. This is particularly crucial for anyone working with exposed wood in their homes or gardens, where appearance matters.
To mitigate this risk, taking a slow and controlled approach to heating wood is essential. Homeowners should be mindful of temperature variations that could affect their project's success and longevity.
Understanding the nuances of how different materials respond to heat treatment not only enhances the ability to choose the right products but also empowers the homeowner to mitigate risks effectively.
Physical Damage During Heat Treatment
In the world of materials engineering, understanding the physical damage that can occur during heat treatment is crucial. This process isn’t just about applying heat; it’s about knowing how different materials respond and what happens when they are subjected to various thermal environments. Physical damages such as thermal expansion and surface degradation can lead to significant consequences, dictating material performance and longevity.
Thermal Expansion
Understanding thermal expansion
When materials are heated, they tend to expand. This phenomenon, known as thermal expansion, is critical to grasp. Every material has its unique coefficient of thermal expansion, which indicates how much it will expand or contract with temperature changes. For example, metals like aluminum expand more than steel when heated. The key characteristic of understanding thermal expansion lies in its predictive ability; knowing how much a material will expand helps in designing components that can withstand these changes without failing.
Cumulative effects over time
Thermal expansion does not just happen during a single heat treatment; its cumulative effects over time can affect material properties. Repeated heating and cooling cycles can lead to fatigue and stress concentrations. For instance, a metal exposed to frequent thermal variations might eventually develop micro-cracks that undermine its integrity. A unique feature of cumulative effects is that they can be subtle, building up over numerous cycles and potentially going unnoticed until failure occurs. This makes regular monitoring essential to prevent surprises later on.
Mitigation techniques
To combat the risks associated with thermal expansion, it is wise to implement specific mitigation techniques. These can include designing parts with expansion joints, using materials with matching thermal expansion rates, or tempering processes that anneal stress. A benefit of these strategies is they provide a proactive approach to managing material behavior under heat. However, the disadvantage comes with added costs and complexity in design, which might not be feasible for every project.
Surface Degradation
Oxidation and corrosion
Surface degradation via oxidation and corrosion poses a significant threat during heat treatment. High temperatures can accelerate oxidation, especially in metals like iron, leading to rust formation. The key aspect of understanding oxidation is recognizing that it can weaken the material, leading to structural failures. Corrosion not only compromises integrity but also is often aesthetically unpleasing. This unique feature of surface degradation requires careful assessments and management strategies, as its implications are severe.
Surface finishes and coatings
In response to the threat posed by oxidation, surface finishes and coatings have become essential. These protective layers can significantly enhance the resilience of materials during heat treatment. The key characteristic of applying surface finishes is their ability to act as a barrier, preventing direct exposure of the material to harmful environmental factors. However, applying these coatings is not without its disadvantages: they can add cost and may require precision in application to ensure effectiveness.
Impact on aesthetics and performance
Finally, surface degradation has repercussions on both the aesthetics and performance of materials. Affected surfaces can become unsightly, detracting from the visual appeal of a finished product. More importantly, the performance can suffer; for example, oxidized surfaces might not function as effectively under load, leading to longer-term maintenance issues. Recognizing the key impact here is crucial for anyone working with materials, especially homeowners looking to minimize future repair costs and enhance longevity.
Chemical Changes Induced by Heat Treatment
Understanding the chemical changes that occur during heat treatment is crucial for grasping how materials respond to elevated temperatures. Decisions regarding heat treatment processes can significantly impact the properties and functional capabilities of various materials. By thoroughly understanding these chemical interactions, stakeholders in construction or DIY projects can better protect their investments and ensure longevity and reliability of the materials they use.
Alloying Effects
Interactions between alloys
Alloys are materials that combine two or more elements, balancing their properties to achieve desired characteristics. The interactions between alloys during heat treatment can lead to enhanced strength and ductility which are beneficial in various applications, such as in construction and machinery. For instance, adding nickel to steel can greatly improve toughness at lower temperatures, making it a go-to choice in many demanding environments.
The beauty of this interaction lies in its adaptability. This means that by selecting the right combination of elements for an alloy, you can tailor the performance of materials to specific needs. However, it is important to note that while alloying can increase performance, it can also introduce complexities in processing due to varying melting points and solidification behaviors, demanding careful control during heat treatment.
Phase transformations
Phase transformations refer to the changes in the structure of a material at various temperature conditions. When heat is applied, materials may undergo significant transformations that can either enhance or weaken their properties. For example, steel that undergoes a transformation from austenite to martensite becomes significantly harder, which can be particularly advantageous in applications like tooling and cutting equipment.
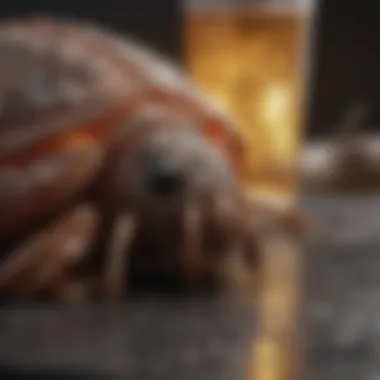
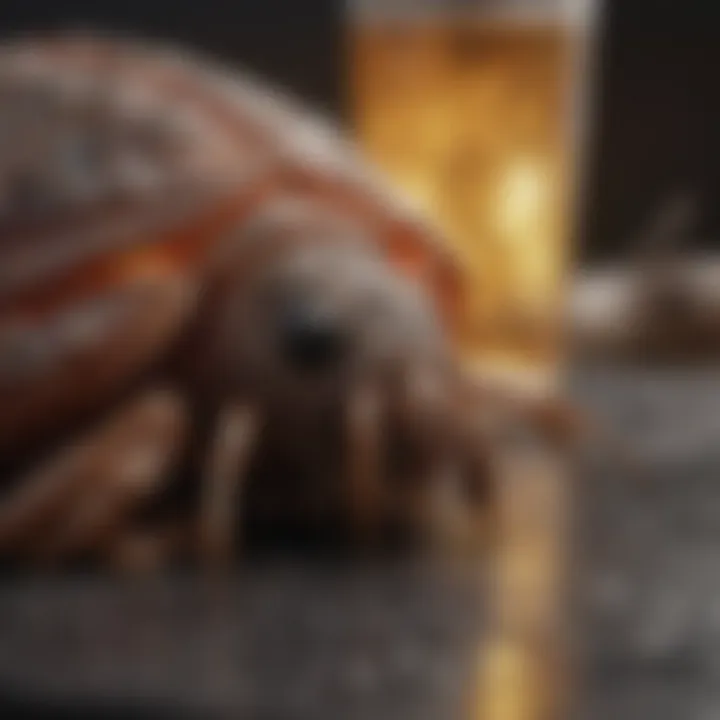
The key characteristic of phase transformations is their capacity to either increase or decrease a material's hardness and toughness. This can be beneficial in fabricating tools that endure wear and tear or detrimental if the resulting material becomes overly brittle. Therefore, recognizing and controlling these transformations during heat treatment can mean the difference between a material thriving in its intended function or failing under stress.
Implications for material characteristics
The implications stemming from changes during heat treatment are far-reaching. Understanding how these chemical changes can affect hardness, corrosion resistance, and overall durability is paramount. For example, heat treatment can relieve internal stresses within a material that may lead to cracking or warping, thereby enhancing its longevity and reliability.
Furthermore, the unique feature of these implications is that they allow for specific customization of the material properties to cater to different environments or requirements. However, while adapting materials for better performance, it’s critical to stay informed about potential trade-offs, such as susceptibility to fatigue or altered thermal properties.
Decomposition of Compounds
Temperature thresholds for decomposition
Decomposition of materials during heat treatment can lead to profound changes in their chemical make-up. Specifically, different compounds decompose at variable temperatures, which has serious implications for integrity and safety. For example, certain plastics might degrade when subjected to high heat, releasing harmful gases. Recognizing these temperature thresholds is crucial for ensuring safe handling and optimal material choice in heat treatment processes.
This characteristic of temperature thresholds allows professionals to make educated decisions regarding the processes to use, which ultimately impacts both material integrity and safety. Being aware of those temperatures helps guide adequately in choosing the right heat treatment method. However, mismanagement can lead to undesirable results, including material failure or environmental hazards.
Impact on material integrity
The impact on material integrity cannot be overstated. When compounds decompose, the structural integrity can be compromised, leading to failure during use. A classic example lies with certain polymers which, once heated beyond their limits, lose functionality and become brittle. This loss directly translates into reduced performance in applications, especially under stress.
An important aspect of this discussion is that, while decomposition can create more malleable materials during processing, it inherently poses risks for long-term use. The challenge lies in balancing the desired malleability obtained from decomposition with the need for maintaining a material's structural integrity post-treatment.
Handling hazardous materials
Finally, the handling of hazardous materials during heat treatment represents both a challenge and a necessity. Certain compounds may emit toxic gases or become unstable when exposed to specific temperatures. Recognizing these hazards provides operators with crucial information for safety protocols and handling precautions.
The crucial feature here is the establishment of stringent guidelines for working with these materials. Not only does this ensure the safety of technicians and customers, but it also preserves the quality of finished products. However, the flipside includes the need for investing in proper safety equipment and training, which can become a financial consideration for smaller operations.
Being mindful of both the chemical changes and the handling of hazardous materials paves the way for safer and more efficient heat treatment processes.
Operational Challenges in Heat Treatment
The realm of heat treatment isn't just about applying heat and waiting for materials to change; it stretches into a world where precision merges with artistry. Understanding the operational challenges in heat treatment is paramount. These challenges can significantly dictate the quality of the final product, impact safety measures, and influence operational costs.
Challenges in this domain touch not just on technicalities but also on practical considerations in a workshop or industrial setting. Recognizing the interplay of temperature control, monitoring methods, and large-scale operational hurdles is crucial for ensuring success.
Monitoring and Control
Importance of precise temperature control
Temperature control is the heartbeat of heat treatment. A slight misstep can result in irreversible damage to the materials involved. When we talk about 'precise temperature control', we're really honing in on the ability to maintain a steady heat level throughout the treatment process. This is instrumental in achieving consistent results, because different materials react differently at varying temperatures. Missing the mark on this can lead to poor mechanical properties or even complete failure of the treated material.
The key characteristic of precise temperature control is its ability to facilitate repeatability in processes. This means that each batch of material treated under the same conditions should exhibit the same properties. Such reliability makes this aspect a highly favorable choice within heat treatment.
However, it comes with its complications. Implementing advanced temperature control systems can be quite costly up front and requires skilled personnel to manage.
Methods for effective monitoring
Delving deeper into the techniques, effective monitoring of heat treatment often relies on real-time data collection and analysis. Utilizing thermocouples or infrared cameras to verify temperature across the material ensures that no part is left out in the cold, so to speak. It’s fascinating how technology, through methods like data logging, can shed light on the heat distribution throughout the process, providing insights into potential issues before they escalate.
The crux of these methods lies in their high level of accuracy. But there’s a caveat; equipment failures or human errors in data collection can lead to disastrous results. The balance between technological reliance and human oversight demands thoughtful consideration in any operational framework.
Challenges with large-scale operations
Scaling up heat treatment operations brings its own set of unique challenges. When you're moving from small prototype runs to full production, the consistency of heating becomes harder to manage. Even small fluctuations can create significant variances in the characteristics of the materials being treated.
One highlight of large-scale operations is the potential for economies of scale. More units often mean lower material costs and faster turnaround times. However, this can also lead to complex logistical challenges. For example, ensuring that each part heats evenly can become a juggling act, especially when using batch processes.
Moreover, the environmental factors can shift drastically at larger scales, creating additional variables that can affect both safety and efficiency. Managing these factors carefully is essential to avoid cascading failures in the production line.
Failure Analyses
Understanding heat-induced failures
Failure analyses dive into the after-effects of improper heat treatment. Understanding how materials fail due to hidden inconsistencies—like micro-cracks or phase shifts—is invaluable for future processes. This aspect usually sheds light on what went wrong, offering critical insights into material behaviors and how to avoid similar pitfalls in the future.
The fascinating part of studying heat-induced failures lies in their diagnostic capabilities; identifying issues early can save time and reduce waste. However, misinterpreting the causes of failure can lead to misguided solutions, and rethinking heat treatment methods may become inevitable.
Case studies and examples
Looking at real-world cases of heat treatment gone wrong can illuminate pathways toward success. For instance, there are notable instances in the aerospace and automotive industries where improper heat treatment led to catastrophic failures in critical components. Each case serves as a reminder of the importance of adhering to prescribed treatment processes.
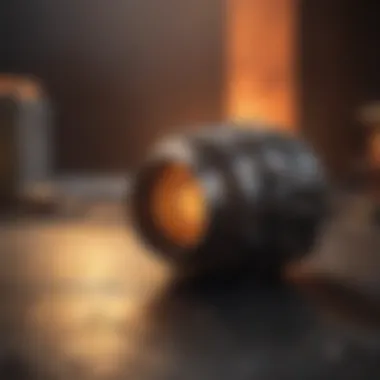
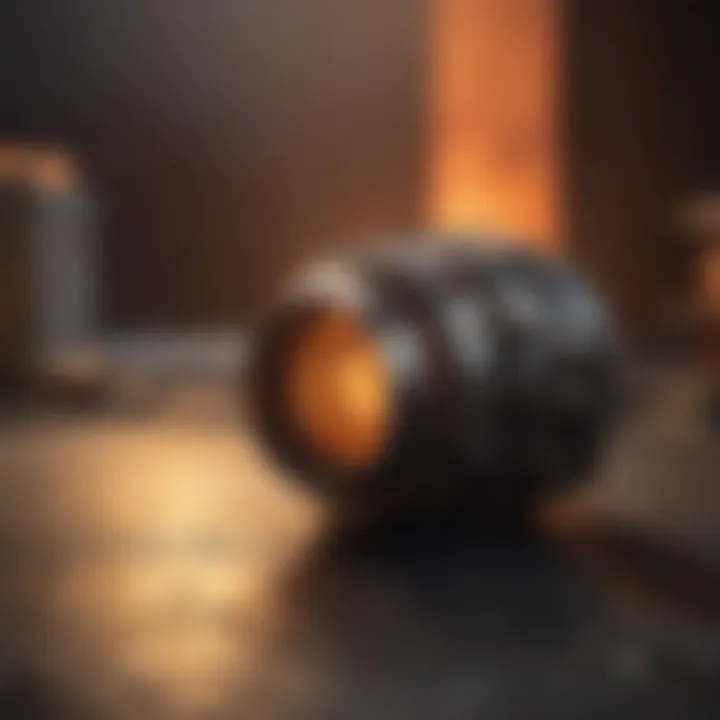
The uniqueness of case studies lies in their practical impact—they serve not just as cautionary tales, but as blueprints. They can guide both novices and seasoned professionals in preventing mistakes. Plus, reviewing these examples fosters a culture of learning and safety within operational environments.
Impact on safety and efficacy
Safety isn't just a checkbox; it's paramount in heat treatment operations. The consequences of failed treatments can extend beyond material integrity to risk employee safety and overall operational efficacy. Understanding the safety implications leads to more robust processes and enhances the credibility of heat treatment methods.
The key characteristic of focusing on safety and efficacy includes establishing protocols to mitigate risks. That could involve routine maintenance checks on equipment or continuous training for personnel dealing with potentially hazardous operations.
Best Practices for Heat Treatment Management
Managing heat treatment processes effectively is crucial for ensuring the desired properties of materials. This section delves into best practices that enhance the quality of heat-treated materials while mitigating risks. From thorough preparatory measures to rigorous inspection methods post-treatment, following these best practices can contribute significantly to long-term performance and reliability of the treated materials.
Pre-Treatment Preparations
Pre-treatment preparations lay the groundwork for successful heat treatment by ensuring that the materials are ready to undergo the changes effectively. Each sub-section here details key procedures that contribute to the overall goal of enhancing material integrity.
Pre-assessment procedures
Before any heat treatment occurs, pre-assessment procedures are essential. This includes evaluating the material's baseline properties and understanding its behavior under heat. Such assessments help identify potential vulnerabilities. Knowing how a material responds to temperature variations aids in setting optimal treatment parameters. A notable characteristic of this process is the diagnostic approach taken, which is often seen as a beneficial method among professionals.
One unique feature of pre-assessment procedures is their focus on identifying phase changes specific to each material type. This reassures the effectiveness of the subsequent heat treatment processes. If neglected, however, misjudgments could lead to structural failures post-treatment, demonstrating its critical role in overall operations.
Material selection criteria
Choosing the right materials to heat treat is critical, as not all substances respond the same way to heat. The material selection criteria include considerations such as chemical composition, existing treatments, and the intended application of the finished product. Focusing on specific properties notably increases the success rate of heat treatments.
This criterion's distinguishing feature is how it aligns with production goals. Materials that meet the right specifications can sustain desired performance after treatment. However, overlooking this aspect may result in high failure rates, undermining the entire heat treatment endeavor.
Environmental considerations
Environmental factors cannot be ignored when preparing for heat treatment. Considerations such as temperature fluctuations in the surrounding areas, humidity, and potential contaminants play an integral role in determining how materials behave during the process.
The key characteristic of this approach is to ensure that the heat treatment environment mimics the ideal conditions as closely as possible. Maintaining control here proves beneficial by preventing unforeseen alterations in material properties. Yet, factors like extreme weather can pose challenges, making it necessary to adapt procedures accordingly to guarantee optimal conditions throughout the treatment.
Post-Treatment Inspections
After executing heat treatment, thorough inspections are crucial in validating whether the process yielded the anticipated results. This section discusses the importance of these inspections.
Ensuring integrity after treatment
One must assess whether the material maintained its intended structural integrity after treatment. This ensures that the heat process did not introduce flaws. The essential aspect of ensuring integrity focuses on the physical attributes of the materials. Implementing this step is beneficial for quality assurance purposes; it can identify potential issues before they escalate.
A unique feature of this process is using non-destructive testing methods, which allows for inspections without damaging the materials. However, if done hastily, it might miss latent defects.
Common inspection methods
Several conventional inspection methods exist, such as visual assessments, ultrasonic testing, and X-ray radiography, each playing a significant role in validating heat treatment results. These techniques help discover imperfections easily, helping professionals maintain quality standards.
A key feature of these methods is their reliability. Many in industries frequently rely on them due to their proven track record. Nonetheless, they often require skilled personnel, which can limit their accessibility in some cases.
Documentation and follow-up
Documentation and follow-up procedures are pivotal. Keeping detailed records of assessments ensures a historical reference to track performance over time. This proves crucial for future projects, as referencing past treatments allows for comparisons and identifies areas needing improvement.
The core characteristic here is transparency; thorough documentation guarantees easy access to necessary information. This can simplify future decision-making. However, the downside can be the time investment needed to maintain thoroughness in records, which some entities might overlook due to operational pressures.
In summary, implementing strong pre-treatment and post-treatment practices fosters a deeper understanding of material behavior during heat treatment, which can ultimately lead to better outcomes.
Culmination
In the realm of material science, the significance of heat treatment cannot be overstated. This process, which can fundamentally alter the properties and behaviors of various materials, plays a critical role in both industrial applications and everyday life. Without a thorough understanding of how heat treatment impacts materials, one might find themselves facing unexpected challenges—be it in a construction project or a home improvement endeavor.
Summarizing Key Insights
To encapsulate the discussions throughout this article, it’s clear that heat treatment is a double-edged sword. While it can enhance strength and durability of materials like metals and plastics, it also presents risks that can compromise their integrity. Here are the key insights:
- Diverse Material Reactions: Different materials exhibit varied responses to heat treatment. For instance, metals often undergo structural transformations that enhance their toughness, while plastics may become brittle or warped with excessive heat exposure.
- Operational Oversight is Crucial: Effective monitoring and control of heat treatment processes safeguard against potential failures and degradation. Whether utilized in homogenization or hardening, precise temperature regulation is key to achieving desired outcomes.
- Best Practices Significantly Matter: Preparing materials adequately before treatment and conducting thorough inspections afterward helps mitigate risks. Simple decisions made at this stage can lead to drastic improvements in both the effectiveness and safety of heat-treated materials.
- Metals: Strengthened through processes such as quenching or tempering, but can develop faults if not carefully monitored.
- Plastics: Can suffer from oxidation or melting when subjected to extreme temperatures, emphasizing the need for appropriate temperature management.
The interplay of heat treatment with material properties is profound, warranting attention from homeowners and industry professionals alike. By grasping the nuances covered in this article, readers are better equipped to approach their projects with an understanding of the critical elements involved.
Future Directions in Heat Treatment Research
As we look ahead, there are several exciting prospects in the field of heat treatment research. Innovations in technology may revolutionize traditional practices, leading to safer and more efficient methods:
- Advanced Monitoring Techniques: The use of digital technologies and machine learning could bring about real-time monitoring systems, making it easier to ensure that materials are treated under optimal conditions without risking degradation.
- Sustainable Practices: With increasing focus on eco-friendly processes, future research might concentrate on finding heat treatment methods that minimize energy consumption and reduce carbon footprints.
- New Materials Development: Ongoing research could yield new composite materials that can withstand extreme heat conditions, enabling advancements in areas ranging from construction to aerospace.
This evolving landscape of heat treatment only emphasizes the necessity for continuous learning and adaptation. Homeowners, DIY enthusiasts, and professionals should stay informed on emerging trends that could bolster the efficacy and safety of their projects. Understanding the future trajectory of heat treatment practices ensures one is not left behind in an ever-advancing field.